What is Porosity in Welding: Secret Elements and Their Influence On Weld Top Quality
What is Porosity in Welding: Secret Elements and Their Influence On Weld Top Quality
Blog Article
Porosity in Welding: Identifying Common Issues and Implementing Ideal Practices for Prevention
Porosity in welding is a pervasive issue that usually goes undetected until it creates considerable troubles with the integrity of welds. In this discussion, we will certainly explore the key aspects contributing to porosity development, analyze its destructive results on weld efficiency, and talk about the ideal methods that can be taken on to decrease porosity event in welding procedures.
Usual Root Causes Of Porosity
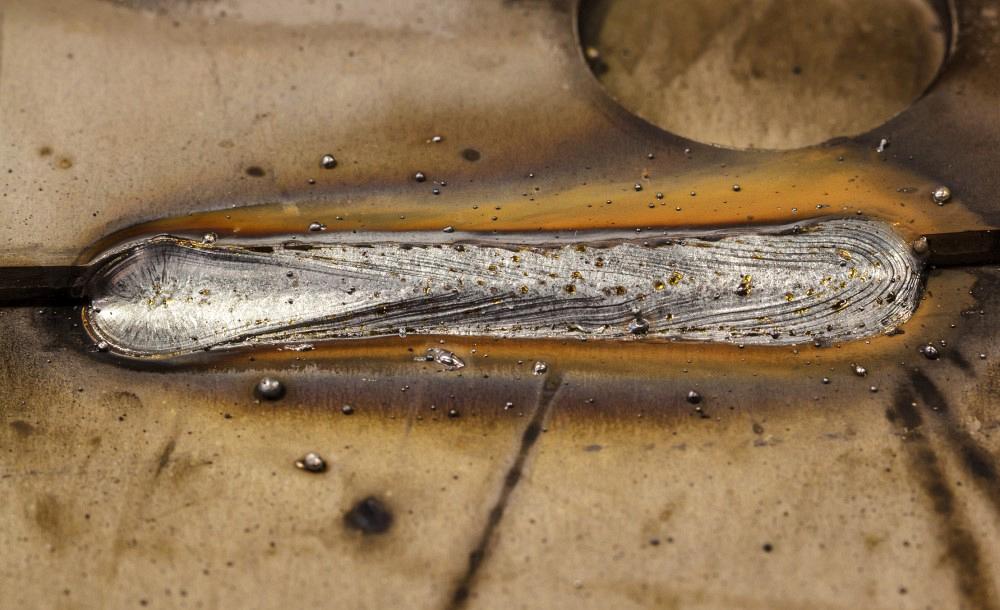
Using dirty or wet filler products can present contaminations into the weld, contributing to porosity problems. To reduce these typical reasons of porosity, thorough cleaning of base metals, appropriate securing gas choice, and adherence to optimal welding parameters are vital practices in attaining top notch, porosity-free welds.
Influence of Porosity on Weld Quality

The existence of porosity in welding can dramatically endanger the structural honesty and mechanical homes of welded joints. Porosity develops voids within the weld steel, deteriorating its general stamina and load-bearing capability.
Among the primary effects of porosity is a decline in the weld's ductility and durability. Welds with high porosity degrees often tend to exhibit lower impact toughness and minimized capability to warp plastically before fracturing. This can be especially worrying in applications where the bonded elements are subjected to dynamic or cyclic loading conditions. In addition, porosity can restrain the weld's ability to effectively send pressures, bring about early weld failure and prospective security hazards in crucial structures.
Ideal Practices for Porosity Avoidance
To boost the structural honesty and high quality of bonded joints, what specific measures can be applied to decrease the occurrence of porosity during the welding procedure? Using the appropriate welding method for the certain material being welded, such as changing the welding angle and gun placement, can even more prevent porosity. Routine examination of welds and immediate removal of any type of concerns recognized during the welding procedure are necessary techniques to avoid porosity and create premium welds.
Relevance of Proper Welding Techniques
Implementing correct welding techniques is extremely important in making sure the structural integrity and high quality of bonded joints, constructing upon the structure of look here efficient porosity avoidance measures. Too much heat can lead to enhanced porosity due to the entrapment of gases in the weld pool. Additionally, making use of the appropriate welding parameters, such as voltage, existing, and take a trip rate, is crucial for achieving sound welds with minimal porosity.
In addition, the option of welding process, whether it be MIG, TIG, or stick welding, ought to line up with the certain requirements of the task to ensure optimal results. Correct cleaning and prep work of the base steel, in addition to choosing the right filler product, are likewise vital parts of skillful welding methods. By adhering to these ideal methods, welders can minimize the risk of porosity development and produce high-quality, structurally audio welds.

Examining and Quality Assurance Steps
Quality assurance actions play a crucial function in confirming the integrity and reliability of welded joints. Evaluating treatments are necessary to detect and avoid porosity in welding, ensuring the stamina and longevity of the last item. Non-destructive testing techniques such as ultrasonic screening, radiographic screening, and aesthetic evaluation are frequently utilized to identify possible problems like porosity. These methods enable the evaluation of this hyperlink weld high quality without compromising the integrity of the joint. What is Porosity.
Performing pre-weld and post-weld evaluations is also critical in preserving high quality control criteria. Pre-weld inspections involve confirming the products, equipment setups, and tidiness of the workspace helpful resources to protect against contamination. Post-weld evaluations, on the other hand, examine the last weld for any kind of problems, including porosity, and verify that it fulfills specified requirements. Executing a thorough quality control plan that consists of extensive screening procedures and assessments is vital to lowering porosity issues and making certain the total top quality of welded joints.
Verdict
To conclude, porosity in welding can be an usual concern that impacts the top quality of welds. By determining the usual reasons for porosity and carrying out ideal practices for avoidance, such as proper welding techniques and testing measures, welders can ensure excellent quality and reputable welds. It is important to prioritize prevention techniques to reduce the event of porosity and maintain the honesty of welded frameworks.
Report this page